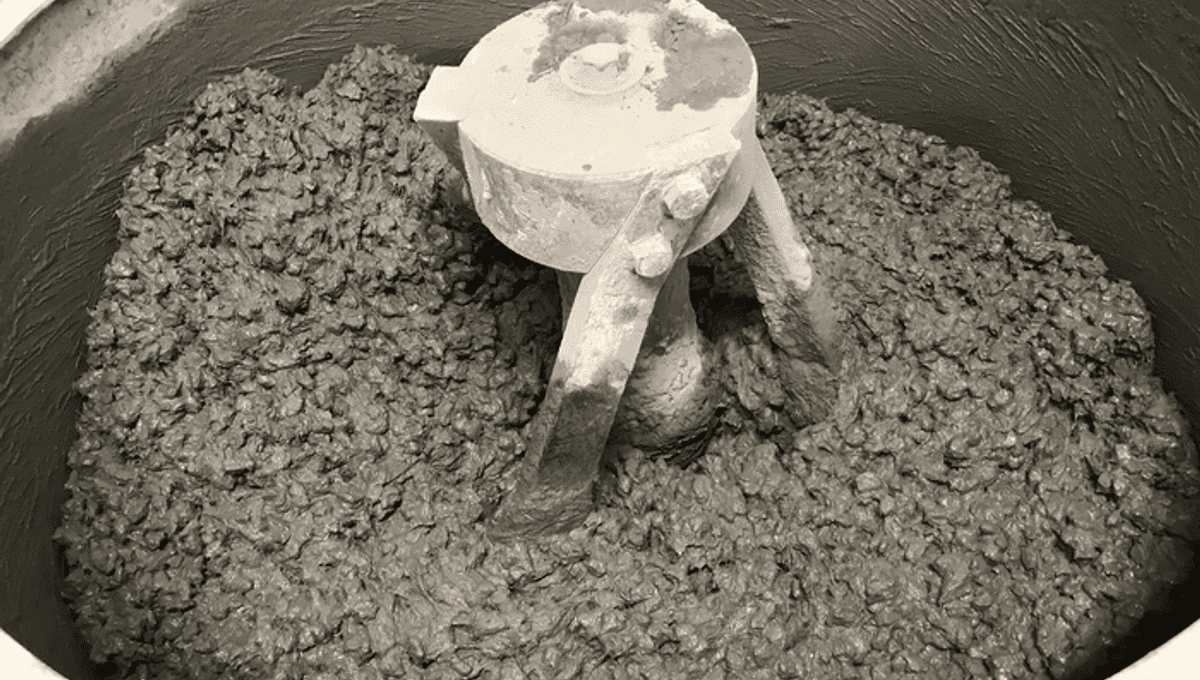
Concrete. It doesn’t sound like a dynamic area of exciting research, does it? Yet it’s seen multiple breakthroughs in recent years: from self-healing concrete using enzymes from human blood, to “living” concrete made from sand and bacteria, to millennia-old concrete that may help save the planet, the science behind the most widely used substance on the planet is constantly evolving to meet today’s challenges.
Challenges like: what do we do with all those used and useless tires that scatter the Earth? Again, it’s probably not something you think about all that often, but the number of waste tires being disposed of each year is set to reach about 1.2 billion by 2030, and they can’t all be chucked on a massive permanent bonfire like in The Simpsons. This “tire graveyard” in Kuwait spontaneously combusted (again) in 2020, spewing toxic chemicals into the surrounding environment.
One solution has been to shred the tires and use the small rubber particles for aggregate in cement – they act as a replacement for some of the traditional ingredients like gravel and crushed rock. But so far, that recycling option has been limited, and attempts to replace all of the aggregates with rubber have produced concretes too weak to meet required standards.
The problem is one of density: crumb rubber is not dense enough to spread out evenly through the concrete mix. On top of that, it’s hydrophobic – it repels water, so even where it is present in the concrete it doesn’t always adhere to the sloppy mixture, creating air bubbles in the finished product. With some parts of the concrete lacking aggregate completely – and other parts lacking even cement – the result is a relatively flimsy, unusable material.
That’s all changed now: a new paper, published in the journal Resources, Conservation & Recycling, describes how to create structurally lightweight concrete whose coarse aggregates are 100 percent rubber from used car tires.
“The technique involves using newly designed casting molds to compress the coarse rubber aggregate in fresh concrete that enhances the building material’s performance,” explained Mohammad Momeen Ul Islam, a PhD researcher in engineering at RMIT University in Melbourne and lead author of the study, in a statement.
“We have demonstrated with our precise casting method that this decades-old perceived limitation on using large amounts of coarse rubber particles in concrete can now be overcome,” he said.
The advantages of the new technique are twofold: firstly, it will cut costs – aggregate accounts for up to 80 percent of concrete, and so sourcing it from discarded tires will naturally remove a chunk of the resources needed to source and process the ingredient from elsewhere.
More importantly, it’s far more ecologically friendly. “As a major portion of typical concrete is coarse aggregate, replacing all of this with used tire rubber can significantly reduce the consumption of natural resources and also address the major environmental challenge of what to do with used tires,” said study co-author and team leader, Jie Li.
The benefits don’t stop after manufacturing: the resulting concrete is lighter than the traditional stuff, making it cheaper and greener to transport to the places that need it. “This would benefit a range of developments including low-cost housing projects in rural and remote parts of Australia and other countries around the world,” pointed out Li.
So should we expect to see used tires being sold to housing developers? Not right away – the new rubber-aggregate concrete may be near twice the strength of previous attempts, but it’s not quite up to code yet. Li and the team are working on making their invention more structurally sound – so watch this space. Concrete is more important than you realize.
Source Link: New Type Of Concrete Uses Old Tires To Beat Environmental Scourge